by Joseph C. Dean, P.E. for the Director, Corrosion Policy & Oversight (DCPO), (DASD) [Materiel Readiness]
Updated: 12-16-2021
Introduction
Within This Page
This resource page provides insights into the importance of good O&M and SRM management and its relationship to CPC. However, it is not the intent of this CPC Source Page to provide a detailed primer on O&M and SRM Management. It is intended to provide insights into how CPC can and should be part of the installation's SRM program on a day-to-day basis, this should help in the planning and development of project work orders and execution.
Corrosion prevention and control (CPC) should play a significant role in facility O&M and SRM processes at DoD installations because, if it is done correctly, facilities will be more durable and sustainable with longer life cycle performance and cost avoidance benefits. CPC SRM engineering and design includes the full range of efforts from corrosion problem identification to selection of criteria and materials, and development of plans and specifications where contract support is planned. For in house shops support, work identification, design, job order description, and execution can provide early and timely CPC problem mitigation. Identification and understanding of design defects, improper materials used, coating failures, and negative construction impacts will help the engineer, architect and maintenance professional determine what corrective CPC measures are required.
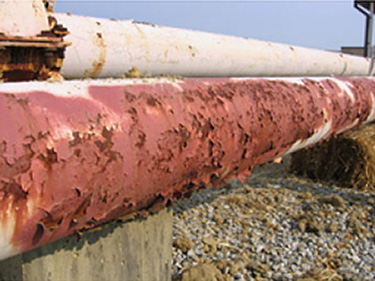
Photo 1: Corroded Pipeline
Source: DCPO Facilities and Infrastructure Corrosion Evaluation Study 2013
These corrective measures may not require full plans and specifications and may be expeditiously resolved using simplified acquisition or utilizing in house maintenance shops support. Discovering the problems before they require extensive costs is an essential feature of good SRM management.
Description
There are four basic methods for control of corrosion: (1) Use materials resistant to corrosion, (2) use protective coatings, (3) use cathodic protection, and (4) modify the operating environment. A well-organized maintenance program should consider approaches to accomplish these four methods along with thoroughly capturing projects through recording workload, planning and conducting emergency and routine repairs, regularly scheduled inspections, preventive maintenance recurring work, and scheduled repair or replacement of facility components as needed to maintain and sustain the facility. In context of this page, Sustainment, Restoration and Modernization (SRM) and Operations and Maintenance (O&M) are used synonymously. In reality, O&M is actually an "Appropriation" category and SRM is a "Project Type" (subset of O&M).
Preventive and predictive maintenance is usually more cost effective than corrective maintenance because materials degrade at a higher rate once chemical deterioration begins, and discovering problems early in the cycle can save resources. Preventive corrosion maintenance can avoid:
- Emergency repair procedures
- Downtime and lost productivity
- Labor and material cost for component removal and replacement
- Shortened service life of the component
The Condition Index Graph (Figure 1) from the DoD BUILDER Sustainment Management System (SMS) contains a typical component-level service-life curve which identifies the economic "sweet spot" for maintenance investment based on the asset (component) condition index. The SMS enables such analysis for each component in the inventory.
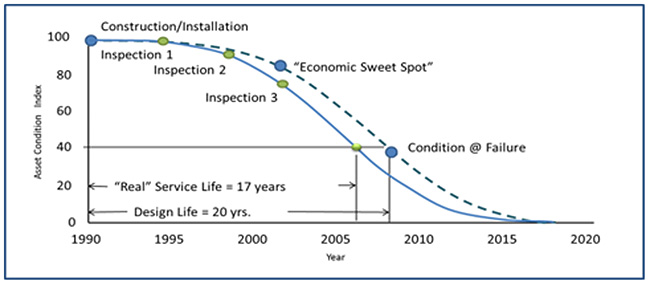
Figure 1: Condition Index Graph
Source: Office of the Deputy Assistant Secretary of Defense (Sustainment)
A good Preventive and Predictive Maintenance Program (see Figure 2) includes the following processes:
- Condition assessment
- Distress survey
- Component material and coatings
- Corrosive environment and severity
- Type and extent of corrosion
- Deficiencies and causative problems
- Maintenance and repair strategies to mitigate corrosion and correct deficiencies
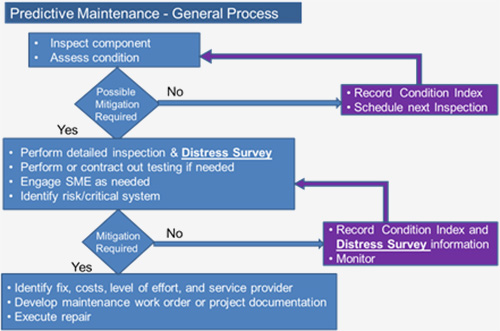
Figure 2: Predictive Maintenance—General Process
Source: Steve Geusic, P.E.
A facilities management program should include CPC. That CPC Program should include budgeting, planning, scheduling, and tracking leveraging well-developed checklists. This enables real-property professionals to make informed and accurate decisions about CPC related facility conditions, workload distribution, and operational readiness requirements. Leveraging the knowledge gained from facilities inspection data and information along with an aggressive CPC education program improves the installation's chances of discovering deficiencies before failure and mission degradation occurs.
Developing and following a CPC Strategy will have a positive impact on the life cycle of facilities. Corrosion should be addressed continuously during the facility life cycle. Corrosion related requirements in specifications and standards should be understood, referenced and distributed to all project team members.
Elements of a good CPC strategy include:
- Establishing good lines of communication within the facilities management team to receive and convey all aspects of CPC and its potential impact to the facility's life cycle costs
- Implementing design best practices for improved life cycle CPC
- Communicating all CPC contract requirements to the Acquisition Team (e.g., Project Manager, Design Manager, Construction Manager, Contractor, Architect/Engineer, Construction Inspector, Quality Control Representative, Sustainment workforce)
- Improving education and training of sustainment personnel in the recognition and implementation of constructed CPC features in the completed project. See the CPC Source Training Page for available resources and insights.
- Inspection and documentation (see the CPC Checklists Tool)
- For more insights into post construction SRM see the next section
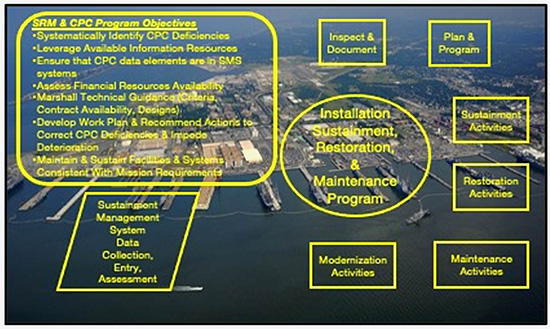
Figure 3: Installation Sustainment Management Program Objectives and Processes
Figure Source: DCPO | Photo Source: MC 1st Class Christopher B. Stoltz / U.S. Navy via Reuters file
Preventive Maintenance, CPC, And SRM Program Management
The extent of facilities corrosion management will vary based upon available financial, manpower, and contracting resources. Modern day facilities management often relies more on predictive modeling for determining requirements rather than prior "hands-on" approaches of utilizing craftsmen and other experts to actually perform visual inspections and tests. Focused inspections include facility types such as cathodic protection and airfield pavements. If "corrosion" is not considered a high priority, then it is very possible that only a failure of a structure or unsightly rust might motivate a repair initiative.
Discovery and timely action to mitigate degradation caused by corrosion will improve life cycle performance. The information collected during routine maintenance inspections, including obtaining advice from journeymen who know the facility well, will help in determining corrosion mitigation strategies. Note that predictive maintenance is a useful tool, but is no substitute for hands-on inspections (visual by maintenance professionals, testing, engineering evaluations), especially in corrosion prone locations (ESC Zones 3-5). This should be considered and addressed in the planning and execution of a maintenance program. For example, the SMS tools could be configured to ensure timely, corrosion-focused, "hands-on" inspections for a targeted list of components based upon the predicted best time for each (see the DoD SMS Section below).
Key questions for the SRM Manager to consider include:
- How is corrosion identified and reflected in inspection and maintenance reports, and captured in information system reports?
- Are corrosion data elements incorporated in the SMS or other facilities software so that an accurate CPC "picture" can be created?
- Are SRM professionals trained to recognize and resolve corrosion deficiencies?
- Are processes in place to ensure that corrosion deficiencies are understood and recorded on a routine basis?
- How is the CPC information used once collected?
- If a contractor provides SRM support, does the government "own" the collected data? Are reports provided by the contractor identifying corrosion deficiencies and resolution?
- Is the CPC Checklists Tool being leveraged?
Suggested resources and actions for the development of the maintenance and SRM program include:
- Design and Construction Processes:
- Construction submittals
- Contracting Officer Technical Representative (COTR) and subject matter expert (SME) interviews and reports
- Architect/Engineer of record design intent
- Contract design criteria and guide specifications
- Design characteristics and geometrics most likely to cause corrosion defects
- Electronic Operations and Maintenance Support Information (e-OMSI) (e.g. as-built conditions, installed information on CPC features, coatings, steel types, material selected and installed, design data and details, and guidance on sustainment actions) (See e-OMSI Scope of Work, Design-Build Model Request for Proposal-Standard Template, and Comprehensive Facility Operation and Maintenance Manual) provided by the Construction Agent during facility turnover. Note: SRM Managers should insist on receiving these essential documents along with systems training to ensure life-cycle sustainability and durability for the life cycle.
- SRM projects should include product and equipment data such as material type, grade, finish, and coating information
- Components and systems should be documented before being covered up/enclosed in walls, foundation, and backfill
- Include photographic documentation
- Ensure that contractor roles and responsibilities have been identified in the contract top support CPC good practice in compliance with UFC 1-200-01 DoD Building Code, UFGS 01 78 23 Operations and Maintenance Data, and UFGS 01 78 24.00 20 Facility Electronic Operation and Maintenance Support Information (eOMSI).
- Installation O&M/SRM Processes:
- Recorded component maintenance and replacement history
- As-built engineering drawings and contract specifications
- Data and information updates should also include changes made during normal day to day sustainment operations
- Records from in house SRM projects
- For existing facilities establish the type and extent of inspection to identify corrosion and other deficiencies and failures. This includes leveraging facility knowledge mentioned and developed in previous bullets (type of materials and coatings used). Based upon this information, corrective measures can be pursued.
- Leveraging the sustainment management system (SMS) to facilitate good, timely, and cost-effective decisions.
- The sustainment management system should:
- Assist with maintenance planning, preventive maintenance scheduling and tracking, corrective work planning and management and cost control
- Support the installation's information system requirements along with providing essential history and SRM program budgeting and scheduling
- Ensure that CPC data elements are included in the SMS and are recordable and reportable
- The sustainment management system should:
Identifying, prioritizing and budgeting for a CPC deficiency or requirement increases the chances of its being identified early. This will facilitate the addition of a specialized CPC feature required in a new or restored facility and increase the chances of being identified in the final RFP and constructed project. The SRM manager must be proactive to ensure that CPC requirements are discovered, addressed and included in all appropriate projects regardless of size and complexity. Corrosion awareness and impacts on operations are key to successful SRM programs. The Facilities Corrosion Impacts on Operations and Missions Table provides high-level insights into specific facilities category corrosion descriptions, contributors to that deterioration and its impacts on operations and mission. Leveraging good engineering knowledge and the Unified Facilities Criteria on the WBDG will help in determining the successful resolution of those deficiencies.
It is recommended that the following CPC Source resources and Tools be viewed and leveraged:
- The Importance of including Corrosion in the Planning Process page provides facilities CPC planning insights.
- For acquisition insights into CPC contract development and management see the Corrosion Prevention and Control Acquisition Issues page. These acquisition basics will help the Facilities Professional navigate key acquisition requirements and pitfalls in the process of achieving a successful CPC contract.
- For insights into design and construction issues see the CPC Design and Construction Issues page.
- For insights into the Facilities Corrosion Impacts on Operations and Mission see the CPC Source Table.
- For a quick reference into project development, planning, project management and evaluation, and CPC Technical details see the CPC Checklists page and associated Checklists Tools page.
CPC Competencies For SRM Management Professionals
Recommended competencies for the sustainment professional will vary based upon many factors including the size and operational tempo of the installation, complexity of the facilities, and location specific environmental severity impacts. The CPC Source Competencies page has been developed to assist in establishing recommended knowledge levels for sustainment professionals engaged in CPC. Pursuit of appropriate coursework to assist in achieving these knowledge and professional levels can be found on the CPC Source Training web page and the linked Facilities Corrosion Knowledge Track Summary . Ensuring that individuals providing CPC services are appropriately qualified via training and certifications is an essential prerequisite for accomplishing durable and sustainable results.
Relevant CPC Criteria Summary
The UFC 1-200-01 DoD Building Code Chapter on Corrosion Prevention and Control, provides very specific guidance for design, construction and sustainment actions related to CPC. The Appendix, ESC for DoD Locations, identifies the Environmental Severity Classification (ESC) Zone for each of the DoD Installations around the world, which then drives the selection of the types of materials and processes that should be used for corrosion-prone locations. The CPC highlights from several of the most relevant UFC and UFGS O&M related criteria include:
-
UFC 3-110-03 Roofing describes the multiple roofing types, materials, roofer qualifications and sustainment options. The UFC must be used in conjunction with the current editions of the National Roofing Contractors Association (NRCA) Roofing Manuals (NRCA Manual) and the NRCA technical bulletins and the Metal Building Manufacturers Association (MBMA) Metal Roofing Systems Design Manual (MBMA Roofing Manual) to provide specific design guidance for Military roofing projects. This UFC explains how to apply the NRCA Manual and the MBMA Roofing Manual to the design of Military projects and the associated limitations and restrictions. There are a variety of materials and roofing systems available. Satisfactory roofing performance comes from careful system and material selection, design, contract document preparation, specification, installation, and maintenance. Roofing systems are exposed to the full brunt of the weather and can allow moisture intrusion or fail prematurely if not properly designed, installed, and maintained. Moisture intrusion can be costly, adversely affect the functions within the building, and result in roof system failure. Since modern roofing systems contain considerable thermal insulation, moisture intrusion lowers thermal efficiency and hinders energy conservation. Wet materials support fungus or mildew, cause deterioration of other roofing system components, and can emit odors leading to sick buildings and occupants. Weathering is mentioned as a term to consider as is corrosion, ultraviolet radiation, durability, and life cycle. The roof design must incorporate systems and details to meet environmental corrosivity conditions for the specific project location, as defined by Environmental Severity Classification (ESC) (See UFC 1-200-01 for ESC designations for DoD worldwide locations and the ICEET Tool). The humidity conditions must be considered during roof design—humid locations are those in ASHRAE climate zones 0A, 1A, 2A, 3A, 3C, 4C, and 5C (as identified in ASHRAE 90.1). The UFC addresses the use of protective metal coatings, types of steel and aluminum and influenced by ESC Zone. Roof asset management with the use of Builder is discussed. The UFC discusses maintenance and the associated inspections required for the creation and sustainment of an effective sustainment program. Identifying, locating and addressing leaks is also discussed. Note that for roofs larger than 15,000 square feet or are classified as "critical use" or "mission critical" a registered roofing consultant (RRC), registered professional engineer, or registered architect is required on the design team.
-
UFC 3-190-06 Protective Coatings and Paints provides requirements and technical guidance for the effective use of paint-type coatings to protect common materials such as metal, concrete, pavements, gypsum board and wooden structures at military activities from deterioration. Requires paints and coatings that are durable and minimize the need for preventative and corrective maintenance over the expected service life of the component or system. Note that this is a significant update from previous versions. Different materials will be used based on local environmental conditions (See UFC 1-200-01). Corrosive environments, which require additional corrosion protection, are those project locations which have an Environmental Severity Classification (ESC) of C3, C4 or C5. Humid locations are those in ASHRAE climate zones 0A, 1A, 2A, 3A, 3C, 4C, and 5C (as identified in ASHRAE 90.1).
-
UFC 3-230-02 O&M: Water Supply Systems serves as a comprehensive O&M manual for on-site field and operations to facilitate easier navigation through O&M of local water supply systems. Addresses several aspects of corrosion and requires the use of UFC 1-200-01.
-
UFC 3-250-03 Standard Practice Manual for Flexible Pavements discusses the importance of pavement maintenance actions, sealers, stabilization, and other useful information concerning mix design, materials, production, and placement of various AC mixtures.
-
UFC 3-250-04 Standard Practice for Concrete Pavements includes the August 1987 Army TM 5-822-7 and the Air Force AFM 88-6 which discusses the realities of the reaction of steel and de-icing salts and corrosion behavior when water is able to gain access. The use of coated dowels and reinforcing steel should be considered in the presence of seawater. Alkali-silica reactions are discussed in this UFC which provides information on their risk, potential damage, and possible solutions. Much has transpired since this UFC was published, including extensive research into heat-resistant mix designs and the categorization and application of ESC Zones (see UFC 1-200-01).
-
UFC 3-260-16 O&M Manual: Standard Practice For Airfield Pavement Condition Surveys discusses spalling, cracking, and foreign object damage (FOD) identification and severity. Both AC and PCC pavements are addressed and identified in a pictorial presentation. It does not address corrosion factors causing these conditions. The value, from a corrosion perspective, is in the understanding of the causative effects of corrosion on surface, edge and cracking.
-
UFC 3-270-01 O&M Manual: Asphalt and Concrete Pavement Maintenance and Repair discusses pavement distresses including cracking, rutting, raveling, or other types of surface deterioration which is indicative of the decline in the pavement's structural load-carrying capacity. Asphalt Concrete (AC) Pavement Distresses are listed. Portland Cement Concrete (PCC) Pavement Distresses addresses the hazards of using gypsum-based PCC (calcium sulfate) repair materials and the presence of free sulfates in the promotion of corrosion in reinforcing steel in pavements. Crack sealing can become a corrosion and FOD problem if not executed properly. UFC 1-200-01 update requires application of new corrosion and related environmental severity guidance and was published after this UFC.
-
UFC 3-270-08 Pavement Maintenance Management encloses Army Technical Manual-563 which describes use and application of the pavement management system (PAVER) developed by CERL. It describes how to establish a PAVER system, condition inspections, maintenance and repair requirements and priorities, data management program and the associated economic analysis for M&R alternatives.
-
UFC 3-410-01 Heating, Ventilating, and Air Conditioning Systems requires the use of UFC 1-200-01, ESC Zone and ASHRAE humidity design guidance. Addresses corrosion requirements, mold growth, and moisture damage. This critically important UFC addresses management of humidity in the building envelop. Failure to accomplish this design objective creates huge potential losses, operational disruptions, health risks, and extensive corrosion damage.
-
UFC 3-420-01 Plumbing Systems addresses corrosion by invoking UFC 1-200-01. Plumbing systems are exposed to corrosion causing conditions and can cause extensive damage when in a failure mode. Plumbing Systems are often installed and function in humid locations as identified in ANSI/ASHRAE/IES 90.1 climate zones. Ensuring that materials and designs are used and implemented that are CPC resilient will save large amounts of funding in repairs and loss of service.
-
UFC 3-430-07 Operations and Maintenance: Inspection and Certification of Boilers and Unfired Pressure Vessels presents basic operation and maintenance guidance on inspection and certification of boilers and unfired pressure vessels. Covers the procedures necessary to determine the material condition of boilers and unfired pressure vessels to ensure their continued safe, reliable, and efficient operation. Corrosion inspection and operation requirements are delineated. UFC 3-430-07 invokes UFC 1-200-01 and has extensive corrosion references.
-
UFC 3-460-01 Design: Petroleum Fuel Facilities addresses corrosion design issues to include impacts of ethanol, hazards related to corrosion, certification issues and tank size, CP, corrosion on underground submerged piping systems, and corrosion resources, guidance and references. Soils shall have a minimum electrical resistance of 50,000 ohm-cm. Foundation material should be neutral or alkaline with a pH greater than 7, a chloride concentration less than 300 ppm, and a sulfate concentration less than 150 ppm as specified by DoD Standard Design AW 78-24-27.
-
UFC 3-601-02 Fire Protection Systems Inspection, Testing, And Maintenance provides requirements for inspection, testing, and maintenance (ITM) of engineered fire protection features in DOD facilities. It is not to be deviated from without prior approval and it cannot be used for acceptance or commissioning of fire protection systems. Corrosion requirements (coatings, materials) and inspections are included. Cathodic Protection systems requirements are addressed.
-
UFC 3-460-03 O&M: Maintenance Of Petroleum Systems provides guidance on corrosion-related inspections for specific system locations, pitting corrosion impacts, and CP systems. This UFC emphasizes inspection and preventive maintenance to avoid system shutdowns, prevent fuel contamination, and decrease fire, safety, and health hazards. Periodic inspections and maintenance are essential to continue efficient safe operations and reduce major repairs. Corrosion is addressed. Refers to UFC 1-200-01 Building Code. Provides insights into corrosion inspections for pantographs, pipe visual inspections, and boom reals.
-
UFC 3-540-07 Operation and Maintenance (O&M): Generators provides guidance and standards for the operations and maintenance of electrical power generators. It includes standard operating procedures, maintenance instructions, and test procedures. Extensive guidance on corrosion related issues such as troubleshooting, inspections, and maintenance procedures is addressed. Refers to the requirements in UFC 1-20-01 Building Code. Corrosion control and mitigation are extensively addressed.
-
UFC 3-550-07 Operation and Maintenance (O&M): Exterior Power Distribution Systems provides guidance for operations and maintenance of electrical power and distribution systems. Electrical systems need regular maintenance to ensure continued compliance with the codes and publications referred to in this document. Such maintenance will prevent system and equipment failures and ensure maximum safety and efficiency in the utilization of the facilities. Contract scope of work should include intervals of performance, methods of application including safety requirements, practices and procedures, and operations and maintenance (O&M) of electrical power and distribution systems. Corrosion is addressed for facility categories such as structures, switches, terminals, connectors, racks, transformers, insulators, bus structures, among others. Recommended corrosion related maintenance actions are included.
-
UFC 3-570-01 Cathodic Protection provides policy and design requirements for CP systems. The UFC provides the minimum design requirements, and must be utilized in the development of plans, specifications, calculations, and Design-Build Request for Proposals (RFP). Note that UFC 3-501-01, Electrical Engineering, provides the governing criteria for electrical systems, explains the delineation between the different electrical-related UFCs, and refers to UFC 3-570-01 for CP requirements. UFC 3-501-01 should be used for design analysis, calculation, and drawing requirements.
-
UFC 3-570-06 Operation and Maintenance Cathodic Protection Systems. This UFC is a "handbook" and provides guidance for inspection and maintenance of CP systems and should be used by field personnel to perform scheduled inspections and preventive maintenance, and to troubleshoot and repair defects.
-
UFC 4-150-02 Dockside Utilities for Ship Service provides design criteria and guidance in the design of utility systems for piers, wharves, and dry docks. Criteria are given for Type I Piers (Fueling, Ammunition, and Supply); Type II Piers (General Purpose Piers); and Type III Piers (Repair Piers). Utilities covered include steam, compressed air, salt or non-potable water, potable water, oily waste/waste oil (OWWO) or petroleum, oil and lubricants (POL), Collection- Holding-Transfer (CHT), electric power, and tele-communications.
-
UFC 4-150-07 Maintenance and Operation: Maintenance of Waterfront Facilities is a guide for the inspection, maintenance, and repair of waterfront structures and related facilities. It is a source of reference for planning, estimating, and performing technical maintenance and repair work; and may serve as a training manual for waterfront facilities maintenance personnel. Corrosion issues are fully addressed including suggested inspection frequencies and locations that includes surfaces, materials, cathodic protection, and locations.
-
UFC 4-390-01 O&M: Unmanned Pressure Test Facilities Safety Certification Manual. This UFC encloses MILITARY HANDBOOK 1039/2 UNMANNED PRESSURE TEST FACILITIES SAFETY CERTIFICATION MANUAL. Requires for Air Force the use of AFMAN 32-1068, Heating Systems and Unfired Pressure Vessels (June 2020) as well. Corrosion is covered extensively in this UFC.
-
UFC 4-750-07 Recreational Aquatic Facilities provides technical criteria and requirements for planning, designing, and constructing natatoria and outdoor aquatic facilities for recreational use. Alteration and renovation projects should update existing facilities to meet this criteria within budgetary constraints. This UFC is intended to promote innovative designs that are functional, economical, safe, aesthetically pleasing, and meet the expectations for modern aquatic facilities. Each design should satisfy the unique requirements of each Installation and at the same time be compatible with the local environment and specific site conditions. Addresses corrosion, micro-climates and invokes UFC 1-200-01.
-
UFGS 01 78 23 Operations and Maintenance Data covers the requirements for Operation and Maintenance (O&M). Submit Operation and Maintenance (O&M) Data for the provided equipment, product, or system, defining the importance of system interactions, troubleshooting, and long-term preventive operation and maintenance. Compile, prepare, and aggregate O&M data to include clarifying and updating the original sequences of operation to as-built conditions. Organize and present information in sufficient detail to clearly explain O&M requirements at the system, equipment, component, and subassembly level.
-
UFGS 01 78 24.00 20 Facility Electronic Operation and Maintenance Support Information (eOMSI) includes requirements for Electronic Operation and Maintenance Support Information (eOMSI). Describes the eOMSI Manual requirements which is required for both Navy and Marine Corps projects. Information to be provided: Product and Drawing Information, Facility Information, and the eOMSI Facility Data Workbook; it is required for Navy facilities operated and maintained under the MAXIMO system. Delete Workbook for Marine Corps, Army, and Air Force facilities. Tailor eOMSI Facility Data Workbook out of this section if it is not used. Additional guidance is provided. Facility managers should ensure that all CPC related construction installed is fully described.
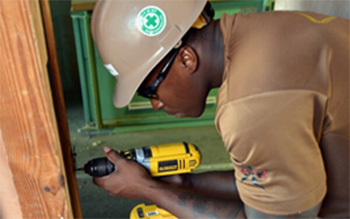
Seabees Repair Coast Guard Training Facility
Source: PO2 Derek Sanchez
DoD Sustainment Management System (SMS) And Facilities Recapitalization Initiative
The DoD has established the SMS as the DoD-wide facility condition assessment process that incorporates the Sustainment Management System for all real property assets. The SMS includes modules such as PAVER, BUILDER, FUELER, and others. Builder™ has the functionality to identify corrosion damage down to the component level with select data fields identifying the distress type, severity level, the quantity/density and a coating condition index. The DoD SMS enables trained building inspectors, engineers, technicians, and maintenance-shop personnel to determine when, where, and how to best maintain facility infrastructure. It provides sustainment experts with real-time, integrated data on the condition, functionality, and remaining service life of DoD facilities, service systems, and components", and, facilitates the development of long and short-range maintenance and repair work-plans, and helps budget for the best investments. The SMS guides facility investment decisions, uses a component-level inventory and condition analysis, and is a useful tool for planning, tracking and improving a wide range of SRM activities. Over time, tools for all asset types will be unified under the Enterprise SMS (ESMS).
The Facility Recapitalization Initiative concentrates on ensuring that warfighter needs are met, either through the use of existing facilities or through the fiscally responsible construction of new facilities. Objectives of the facility recapitalization program includes:
- Sustaining existing facilities
- Achieving inventory-wide facility condition index (FCI) goals
- Ensuring that all DoD facilities are capable of meeting mission requirements, and, providing a reasonable quality of life to DoD personnel
- Establishing methods to identify and remediate failing facilities in poor physical condition, through demolition, replacement, or repair
CPC, O&M And SRM Summary
CPC sustainment actions must be in line with the installations' facility life cycle objectives to ensure sound budgeting and wise expenditure of what is often a very limited sustainment budget. Several considerations for the sustainment engineer, architect and maintenance professional include:
-
Identify and leverage the Installation's ESC Zone(s) for a new or renovated facility, incorporate more corrosion resistant materials and features
-
Develop a CPC Preventive Maintenance Strategy as part of the broader installation O&M and SRM Program
-
Ensure that the CPC Inspection Program checks (see CPC Checklists) for design geometry deficiencies
-
Conduct inspections and data capture to include the type and extent of corrosion, component material, coatings, warranties, age, and maintenance history
-
Research best practices discovered by other facilities management organizations, listed on the WBDG and in criteria
-
Ensure that CPC goals, objectives, and actions support operations and mission
-
Conduct CPC training for mechanics and inspectors
-
Ensure that facility turnover includes discussion and documentation of CPC features included in the constructed project
-
Consult Service subject matter experts (The Engineer Research and Development Center, Construction Engineering Research Laboratory, (ERDC-CERL), Naval Facilities Engineering and Expeditionary Warfare Center (NAVFAC EXWC), and Air Force Civil Engineer Center (AFCEC). There are also SMEs that are part of the UFC program discipline working groups (DWGs) for each service.
- Understand CPC specialty (knowledge) areas and review the content included in the CPC Knowledge Areas on the CPC Source:
- Cathodic Protection
- Corrosion Science
- Paints and Coatings
- Waterfront and Coastal Structures
- Piers and Wharves
- Aviation Facilities and Support Structures
- Utilities and Buried Structures
- Petroleum, Oil, And Lubricants (POL) Storage and Distribution Systems
- Fencing
- Doors
- Asphalt Concrete and Portland Cement Concrete Pavements
-
Ensure that the SRM Engineer is involved in problem identification and solution development
-
Ensure participation in developing contract requirements, scope, and review of selection factors
-
Ensure that the planning and estimating associated with CPC project development is accurate and complete
-
Ensure that the maintenance force is trained in relevant CPC topics (see Facilities Corrosion Knowledge Track Summary and DoD Continuing Education on the WBDG)
-
Ensure that e-OMSI data and information is accurate and recorded in the installation's information resource repository and is easily available to the SRM Engineer, maintainers and associated support contractors
-
Understand the role that cleaning and maintenance plays in preventing corrosion; this includes avoiding the accumulation of debris, blocking of drains and deferring painting in lieu of cleaning
-
Regularly monitor the CPC health of the facilities (see CPC Checklists)
-
Monitor in place detection systems such as cathodic protection and Supervisory Control and Data Acquisition (SCADA) Systems
-
Leverage CPC information systems knowledge to develop accurate, defensible budgets and maintenance plans
-
Ensure that the Government Sustainment Engineer/Architect establish in the contract the expectations for CPC and associated proficiency levels of contractor employees to ensure that CPC solutions are correctly delivered
-
Require consistent and complete recording of work planning, execution and completed documentation in the SMS/installation facilities management data systems for both contractor and government maintenance personnel
ADDITIONAL RESOURCES
Department of Defense — Whole Building Design Guide
Unified Facilities Criteria (UFC) (See Relevant CPC Criteria Section Above for a More Complete List)
- UFC 3-110-03 Roofing
- UFC 4-150-07 Maintenance and Operation: Maintenance of Waterfront Facilities
- UFC 3-460-03 O&M: Maintenance Of Petroleum Systems
- UFC 4-860-03 Railroad Track Maintenance & Safety Standards
Unified Facilities Guide Specifications (UFGS)
- UFGS 01 78 23 (August 2015) Operation and Maintenance Data
- UFGS 01 78 24.00 20 Facility Electronic Operation and Maintenance Support Information (eOMSI)
- See UFGS (for a complete listing)
DoD
- Facilities Sustainment Model (CAC Access Only)
- Sustainment Management System Suite of Tools
- DoDM 7000.14-R Department of Defense Financial Management Regulation (DoD FMR)
U.S. Army Corps of Engineers
- Army TM 5-624 et al Maintenance and Repair of Surface Areas
- Builder and the Sustainment Management System
- Construction-Operations Building Information Exchange (COBie)
Naval Facilities Engineering Command
- NAVFAC Building Information Management And Modeling (BIM) & Facility Electronic Operation And Maintenance Support Information (eOMSI) Program
- MO-406 Hyperbaric Facilities Maintenance Manual
- MO-104.1 Maintenance of Fender Systems and Camels
General Service Administration (GSA)
Other WBDG Resources
- WBDG Resource Pages
- Facilities Operations & Maintenance
- Comprehensive Facility Operation & Maintenance Manual
- Reliability-Centered Maintenance (RCM)
- Critical Equipment Identification and Maintenance
- Optimize Operational And Maintenance Practices
Tools
Publications
- FEMP Operations & Maintenance Best Practices, Release 3.0: A Guide to Achieving Operational Efficiency
- AMPP—NACE/SSPC TG-527 Joint Standard Practice "Corrosion Prevention and Control Planning Standard" (Hosted on the AMPP Website)
Training
- WBDG04 Optimizing Operations and Maintenance (O&M)
- CPC Source Training Page
- Facilities Corrosion Knowledge Track Summary
- CPC Competencies
- Continuing Education (CPC Training)
Organizations
- Advanced Surface Engineering Technologies for a Sustainable Defense (ASETSDefense)
- American Concrete Institute
- American Institute of Steel Construction
- Association for Materials Protection and Performance (AMPP)
- American Public Works Association
- American Society of Civil Engineers
- American Society for Testing and Materials (ASTM)
- American Society of Heating, Refrigeration, and Air-Conditioning Engineers
- The American Society of Mechanical Engineers
- American Institute of Timber Construction
- American Water Works Association
- Asphalt Institute
- Defense Acquisition University (Corrosion Community of Practice)
- International Facility Management Association
- National Association for Surface Finishing (NASF)
- SAE International